How Wall Loss & Tube Leaks Impact Vessel Efficiency
To get the best performance out of a vessel it’s important that it maintains necessary operating capacity. While there are several preventative maintenance procedures that can prolong the life of the vessel, eventually a decision on retubing or replacing the unit will need to be made. Tube wall loss, tube punctures, deposit build-up, a catastrophic failure can all contribute to reduced operating efficiencies. As a result, it’s important to understand when a unit needs to be evaluated and methods for prolonging replacement.
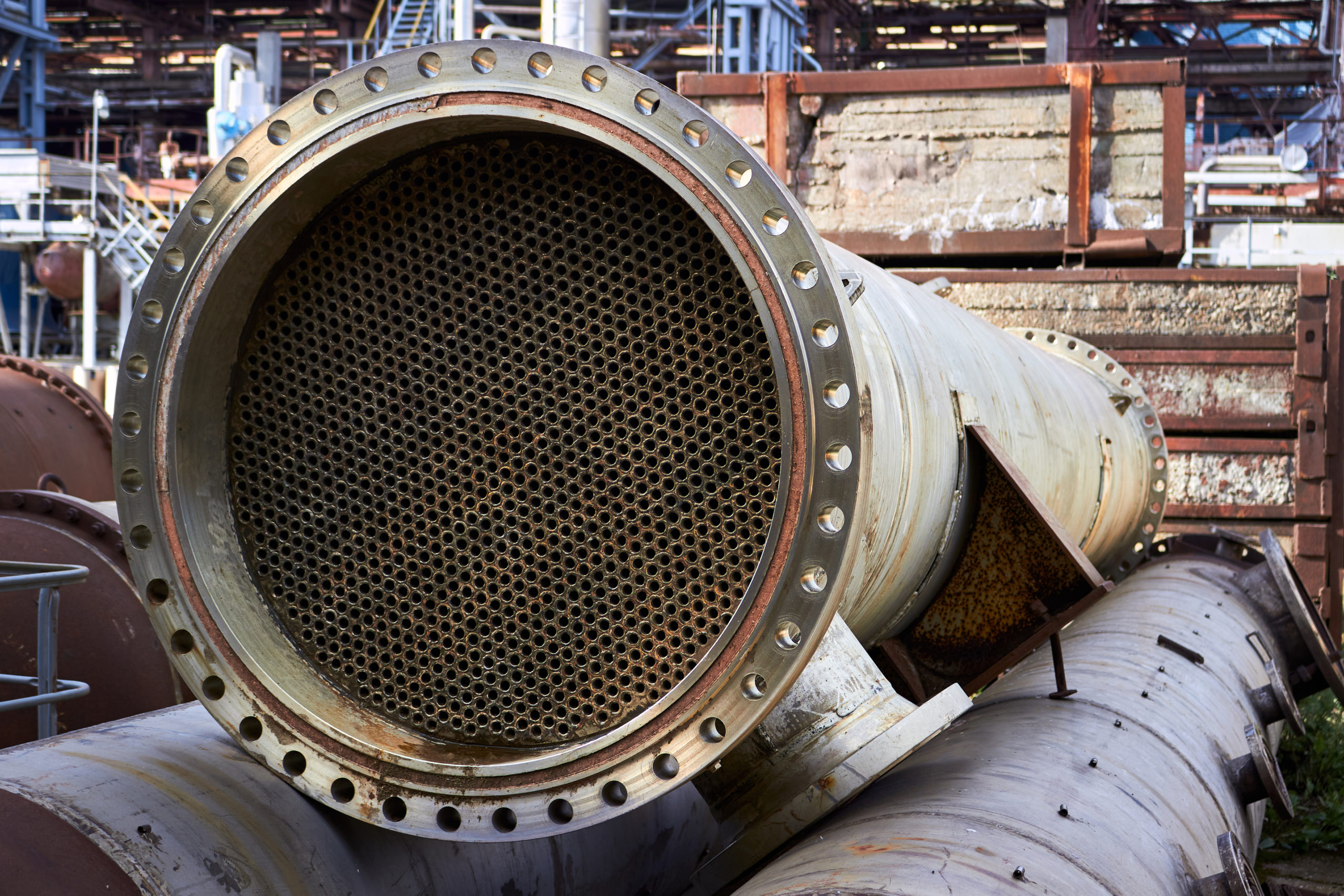
Vessel testing is generally conducted using eddy current testing in heat exchangers or ultrasonic testing in boilers. If testing reveals significant tube wall loss, tubes can be plugged, sleeved, lined, or replaced. The type of action required usually comes down to the age of the vessel, the application it’s being used in, and the budget an organization has for maintenance.
In heat exchanger applications, vessels are typically built with a 10 – 15% surplus capacity. This means that when tubes are plugged or clogged with debris, it can still maintain an overall operating efficiency of 100% until it’s reached 10 – 15% of the vessel. While there may be certain applications where a vessel does not need to maintain 100% capacity, in higher production facilities like refineries, the goal is to be operating at the maximum limit to keep up with demand.
Once the operating efficiency of an exchanger is below 100%, many customers will look at next steps. Often refineries will have one or two back up exchangers that can take over in the event of a catastrophic failure or planned maintenance schedule. In these situations, the vessel that needs maintenance can be turned off, pulled, and shipped out to a fabricator for service.
Depending on the amount of damage to the tube, sleeving or lining can be a great way to reduce cost and labor. A sleeve is a short section of tube that is expanded into the tube end and tube sheet, to extend the life of the tube end. These are used when there is wear at the tube sheet, generally on the inlet side of the vessel. Similarly, a liner is a full-length patch that is used when there is wall loss throughout the tube. This is installed by hard rolling at the end of the tube sheet, then sealed to the entirety of the tube using hydrostatic pressure.
If the amount of wall loss in the vessel is too extreme for sleeving or liners, the vessel will either need to be completely retubed or replaced. Retubing presents several challenges, due to the uncertainty of sizes and conditions. If the costs are too high, vessels may be scrapped in favor of a new one. However, in some cases, retubing may be the most economical decision. For example, when it comes to exotic materials like Hastelloy, Inconel, or titanium, it can be a lot easier to preserve the tube sheet and do a full retube. This is due to limitations in sourcing material, as well as the cost of machining it.
While similar to heat exchanger applications, boilers can typically go longer between retubes or replacements depending on the type of fuel used. With cleaner fuel sources and better tube materials, boilers will experience less deposit build-up, prolonging the life of the tubes. If a boiler does experience leaks or extreme wall loss, many customers will opt to plug or replace tubes on an as needed basis. After so many tubes have been plugged, the boiler will either need a full re-tube or be replaced.
Overall, it’s important that a vessel is working as close to 100% capacity as possible, to maintain efficiencies and reduce unexpected outages. Once wall loss or tube leaks begin to impact the efficiency of the vessel, preventative maintenance steps will need to be taken. This can range from sleeving the vessel to a full retube of the unit. As a result, it’s important to understand when a unit needs to be evaluated and the different options available for repair.